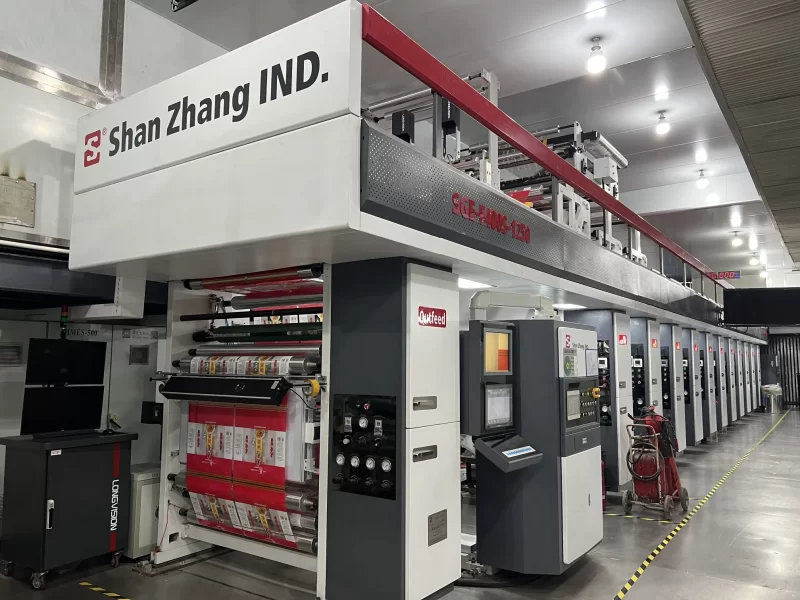
Fleksibel emballage has nowadays become the benchmark for state-of-the-art, high-speed, and multi-service packaging. From food and beverage to pharmaceutical and industrial usages, the manufacturing process of packaging requires a somewhat sophisticated and accurate flexible packaging manufacturing process. This blog covers the 9 major steps involved in the manufacturing process of packaging solutions and clearly explains the process through which flexible packaging products are produced efficiently and sustainably.
What is Flexible Packaging?
Fleksibel emballage refers to packaging made with flexible materials, which can usually be changed and adjusted according to the shape of the product. It is mainly made of flexible materials such as plastic film, paper, metal foil, etc., through printing, laminating, bag making, and other processes, used to protect, store and transport a variety of products.
Flexible Packaging Manufacturing Process
Fleksibel emballage has nowadays become the benchmark for state-of-the-art, high-speed, and multi-service packaging. From food and beverage to pharmaceutical and industrial usages, the manufacturing process of packaging requires a somewhat sophisticated and accurate flexible packaging manufacturing process. This blog covers the 9 major steps involved in the manufacturing process of packaging solutions and clearly explains the process through which flexible packaging products are produced efficiently and sustainably.
Step 1: Your Order – Initiating the Packaging Manufacturing Process
The process begins with understanding client requirements and order confirmation. Clients provide specific details, including design, material preferences, and sizes. This step sets the stage for the smooth production of packaging tailored to each business’s needs.
Step 2: Cylinder Making – The Foundation of Precision Printing
Cylinder manufacturing is a critical step for ensuring high-quality prints. Cylinders are created to replicate the design accurately. This precision ensures that all subsequent stages of the Flexible Packaging Production Process align perfectly with the design specifications.
Step 3: Printing – Bringing Designs to Life
Using high-speed printing machines, designs are applied to the chosen packaging material. Skilled engineers monitor the process to maintain the consistency and vibrancy of the printed visuals. High-quality inks ensure clarity and long-lasting color, a key requirement in manufacturing packaging that stands out.
Step 4: Printing Inspection – Quality Assurance Before Lamination
After printing, every roll undergoes a thorough inspection to guarantee flawless print quality. Any defects are identified and corrected before moving forward in the Packaging Manufacturing Process.
Step 5: Solvent-Less Lamination – Ensuring Material Bonding
Lamination is where multiple layers of flexible packaging material are bonded together. Advanced solvent-less technology ensures environmental safety while maintaining strong adhesion. This step enhances durability, which is essential in Flexible Packaging Manufacturing.
Step 6: Curing – Strengthening Adhesion
Curing involves precise control of temperature and time to ensure the laminated materials bond effectively. Scientific curing techniques create strong, flexible packaging materials capable of withstanding various stresses.
Step 7: Slitting – Precision Cutting for the Perfect Fit
In this stage, large rolls of laminated materials are slit into smaller widths to meet specific product requirements. Accurate slitting ensures seamless progress in the Flexible Packaging Production Process, avoiding issues during subsequent stages.
Step 8: Bag Making – Crafting the Final Product
State-of-the-art machinery transforms flexible materials into a variety of bag types, be it stand-up pouches, zip-lock bags, or specialty packaging. The result of this stage is the completion of packaging products customized for diverse industries.
Step 9: Bag Inspection & Packing – Final Quality Control
Every bag undergoes rigorous inspection to ensure it meets industry standards. This critical step ensures that only high-quality packaging products are shipped to customers. The goods are packed efficiently and prepared for delivery.
Konklusion
The production of flexible packaging involves a meticulous series of 9 critical steps, from order initiation to final delivery.
The Huiyang Flexible Packaging manufacturing process combines state-of-the-art machinery, expert kvalitetskontrol, and precise execution to deliver products that meet the needs of a wide range of flexible packaging markets. By following these nine key steps, companies can ensure the delivery of high-quality, sustainable, and cost-effective Tilpassede fleksible emballageløsninger.