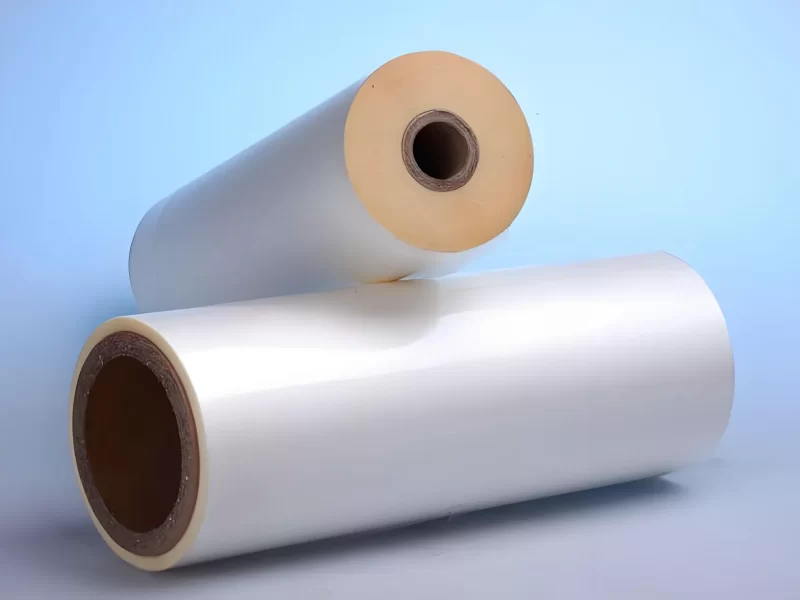
Laminated packaging, a packaging form that cleverly combines multiple layers of materials, relies heavily on the scientific matching of materials and their complementary performance. Each material possesses unique physical, chemical, and functional properties, and when combined properly, it can meet the packaging needs of various products while enhancing the overall performance of the packaging in all aspects.
Core Materials of Laminated Packaging
Laminated packaging bags are typically made of two or more materials through the lamination process. Common core materials include BOPP, CPP, PET, AL, PE, PA, and PAPER. Below are the characteristics of some of these commonly used materials in flexible laminated packaging.
BOPP (Biaxially Oriented Polypropylene)
BOPP is a popular material for laminated packaging films due to the following characteristics:
- High Transparency: BOPP film offers excellent transparency, allowing the items inside the laminate package to be displayed.
- Excellent Mechanical Strength: BOPP boasts good tensile and tear resistance, ensuring the protection of the internal products.
- Good Heat Sealing Performance: BOPP is easy to heat-seal with other materials, forming a reliable and stable seal.
- Improved Barrier Performance: Although BOPP alone offers limited barrier properties against oxygen and moisture, its overall barrier performance is significantly enhanced when laminated with other materials.
CPP (Cast Polypropylene)
CPP film is known for its flexibility and low production cost, making it ideal for flexible laminated packaging applications:
- Good Flexibility: Suitable for packaging that requires folding or bending, CPP offers good flexibility and impact resistance.
- Excellent Heat Sealing Performance: CPP forms a reliable heat-sealed structure with other materials.
- High Transparency: Ideal for packaging that showcases the contents, ensuring clarity.
- Chemical Corrosion Resistance: CPP is resistant to most acids, alkalis, and solvents, making it suitable for laminated packaging for chemical products.
- Cost-Effective: CPP is relatively inexpensive, making it a good option for the large-scale production of laminated packaging pouches.
Polyester (PET)
PET is one of the most commonly used materials for laminated packaging films, known for its robust properties:
- High Strength and Rigidity: PET has excellent tensile and tear resistance, protecting internal products.
- Chemical Resistance: It tolerates most acids, alkalis, and solvents, making it ideal for laminated packaging for food products.
- Environmentally Friendly: PET is recyclable, aligning with the growing demand for sustainable flexible packaging lamination processes.
- Recyclable: PET’s recyclability supports environmental sustainability efforts in packaging design.
Aluminum Foil
Aluminum foil is a vital material in laminated packaging films that require high-barrier properties:
- Excellent Barrier Performance: It provides a solid barrier against oxygen, moisture, and light, significantly extending the shelf life of products.
- Good Heat Sealing Performance: Aluminum foil forms a smooth, easily heat-sealed structure with other materials.
- Relatively High Cost: Although more expensive, laminated aluminium foil packaging is indispensable in scenarios requiring high-barrier protection.
Polyethylene (PE)
Polyethylene is frequently used as an inner or outer layer in laminated packaging bags due to its cost-effectiveness and protective properties:
- Good Sealing Performance: PE’s excellent heat-sealing capability ensures the formation of a reliably sealed structure.
- Flexible and Impact-Resistant: PE is soft and impact-resistant, offering protection against external damage.
- Cost Advantage: Its relatively low price makes it suitable for large-scale production of laminated food packaging.
- Chemical Resistance: PE withstands most chemical substances, making it ideal for packaging liquids or powders.
Nylon (PA)
Nylon, often used to enhance barrier properties, brings the following features to laminated packaging films:
- Superior Barrier Performance: Nylon is highly resistant to oxygen and moisture, extending the shelf life of products in laminated packaging for food.
- High Strength and Durability: It offers excellent tensile and tear resistance, making it suitable for high-strength packaging requirements.
- Good Heat Sealing Performance: Nylon is easy to heat-seal with other materials, forming a stable structure.
- Higher Cost: Although the cost is relatively high, its value is essential for products requiring enhanced barrier and strength properties.
Paper/Fiber Materials
Paper is often used in laminated paperboard packaging to improve the aesthetic appeal and environmental friendliness of packaging.
- Good Printing Performance: The smooth surface of the paper makes it perfect for high-quality printing, enhancing brand visibility.
- Environmentally Friendly: Paper is easy to recycle and decompose, supporting sustainable packaging practices.
- Low Cost: Paper is cost-effective and suitable for mass production.
- Weak Barrier Properties: Paper typically requires lamination with other materials to compensate for its poor barrier performance.
Conclusion: The Future of Laminated Packaging
Laminated packaging films effectively meet the diverse needs of various industries by utilizing the complementary performance characteristics of each material. As the world focuses more on environmental sustainability, laminated packaging materials will increasingly emphasize eco-friendly properties. With innovations in lamination in packaging, flexible packaging laminate structures, and laminating adhesives for flexible packaging, the laminated packaging industry is poised for continued growth.
This evolving trend aligns with the need for environmentally friendly laminated packaging and presents new opportunities for the development of packaging solutions that combine function with sustainability. As consumer demand for eco-conscious products increases, laminated food packaging and other sustainable options will take center stage in the packaging sector.